Anyone who’s been in the business world for any length of time has heard of continuous improvement. The concept is simple and self-explanatory. What may be less obvious is how many of the benefits of continuous improvement are connected to one another.
While not all of the benefits are a direct result of another, there’s an obvious correlation. One benefit can directly or indirectly impact another. As a result, many benefits of continuous improvement can have a snowball effect.
Let’s start by looking at continuous improvement on a high level.
14 Benefits of Continuous Improvement
1. More Efficient Operations
2. Higher Productivity
3. Shorter Delivery Times
4. Lower Error Rates
5. Higher Quality
6. Increased Innovation
7. Lower Costs
8. Increased Profitability
9. Better Working Environment
10. Happier Employees
11. Lower Employee Turnover
12. Improved Culture
13. Better Customer Experience
14. Increased Brand Reputation
When you look at a list of benefits, you can see how many of these likely have a direct impact on others. Continuous improvement efforts in one area can produce efficiencies, which also have an indirect impact on other areas.
Continuous Improvement Methodologies
LEAN methodologies like Lean Six Sigma focus on removing processes that don’t add value to the final product. Specifically, they aim to remove waste and variation from the process. To illustrate, the primary focus areas are represented by the acronym DOWNTIME.
(D)efects
(O)ver-Production
(W)aiting
(N)on-Utilized Talent
(T)ransportation
(I)nventory
(M)otion
(E)xtra-Processing
Not everyone utilizes a formal methodology or program. That’s okay because establishing an official program isn’t required to reap the benefits of continuous improvement. All that’s required is a concerted effort to analyze your operations and apply some common sense. If you’re versed in LEAN concepts, then that’s even better.
Sometimes that’s as simple as watching a process to identify where time and resources are being wasted.
In addition, don’t make the mistake of thinking that these principles only apply in a manufacturing or distribution environment. While they may be most commonly applied there, you can use them in any business environment.
It’s about the process, not the product, service or task you’re engaged in.
LEAN concepts can be applied to any task in any business. It doesn’t matter what industry you’re in because these principles can be applied to everything from manufacturing to banking to dentistry.
For the sake of simplicity, I’m going to refer to everything as a product.
If you make plastic bottles, that’s a product. Plumbing repair? That’s a product. Life coach? You guessed it. Also a product.
Now that we’ve talked a little about the concepts, let’s take a look at each of the benefits in more detail.
More Efficient Operations
The first and most obvious benefit of continuous improvement is that you will have more efficient operations. When you remove wasted motion, unnecessary tasks, and time-consuming components, your processes become more efficient and effective.
Once again, you don’t necessarily have to implement a formal program. However, you do need to understand the concepts enough to identify where you can make changes.
Key Benefits: Reduced labor costs, lower cost to produce your product or service
Higher Productivity
When you eliminate steps that don’t add value, you make your process more efficient. This added efficiency naturally results in a reduction in the time it takes to complete a given task. As a result, you’ll be able to complete more tasks in the same amount of time.
Key Benefits: Higher production capacity, reduced labor costs, faster delivery
Shorter Delivery Times
When you produce your product in less time, you can get it into your customers’ hands sooner. The faster you produce your product, the sooner you can deliver it to your waiting customer. The result is a shorter overall lead time for customers.
Key Benefits: Higher output, faster delivery, happier customers
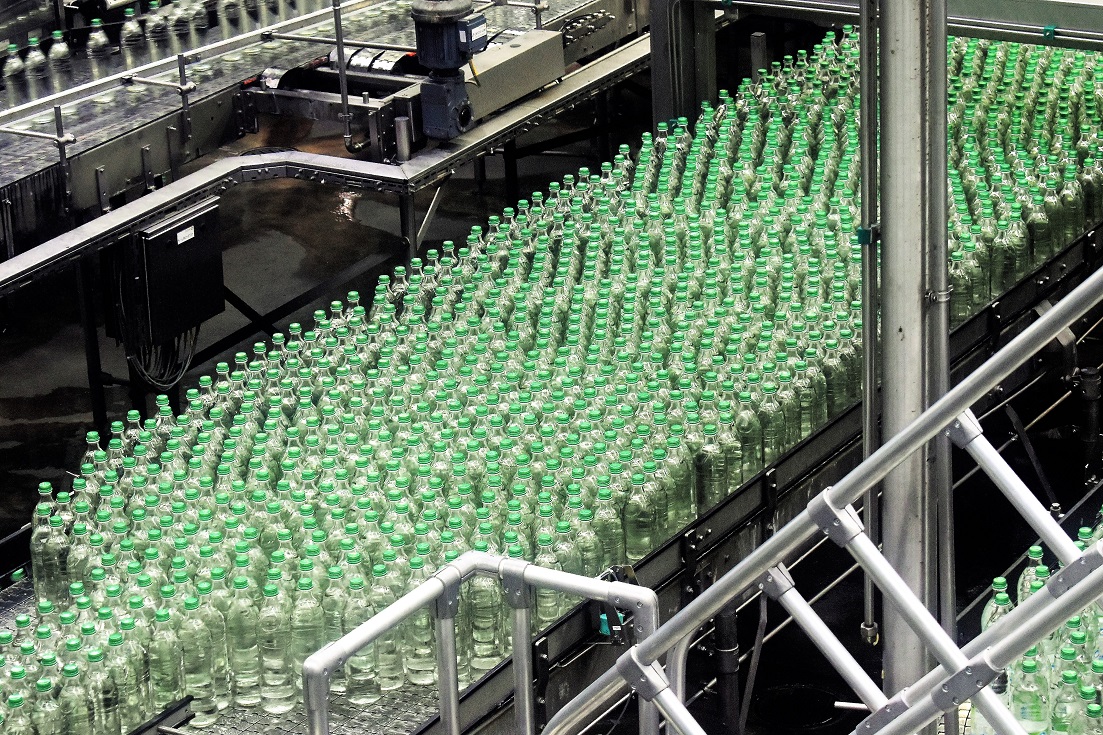
Lower Error Rates
The continuous improvement process results in refining your processes. When you refine how you do something, you naturally get better at it. As a result, you reduce the number of errors.
Refined process = better process = fewer mistakes = better quality control.
Key Benefits: Better quality control, less wasted time/material, fewer negative customer experiences
Higher Quality
When you improve your process, the result is a higher quality product, which has multiple benefits. Firstly, the obvious benefit is the prior point. There are fewer mistakes. As a result, you make gains in labor, material and customer perception. Just as important, there are also fewer customer returns and negative customer experiences.
Secondly, the perception of your quality is increased. This increases the reputation of your brand. Nobody wants to buy something only to find that it doesn’t work as intended. Customers appreciate the reliability of your product and your reputation will improve accordingly.
Key Benefits: Lower return rate, improved market positioning, higher brand reputation, increased ability to charge a premium price for your product
Increased Innovation
Improving processes is not only about removing waste. Often, you’ll be finding a better way to do something. Many of these innovations are small, but sometimes you’ll invent a completely new way of doing something. This can create a seismic shift in how you do business.
I once worked with a company that created such a seismic shift. When attempting to address some operational issues, the team decided they needed to think “outside the box”. As a result, they completely discarded the industry norms. No idea was too crazy. When someone asked “why?”, they responded, “why not?”.
The resulting changes were such dramatic improvements that they gained a competitive advantage that kept them on top of their industry for years.
Key Benefits: More opportunities for innovation, improvement in the culture, competitive advantage
Lower Costs
As you would expect, when you produce more product, in less time and with fewer errors, you reduce your costs. The additional productivity combined with the time savings reduces your labor expense.
If you manufacture something, you’ll also save on material costs. You can use less material by utilizing your raw materials more efficiently. You also reduce waste caused by production errors.
(Here’s another post that may give you some ideas about how to reduce your costs.)
Key Benefits: Increased profitability, reduced working capital, better cash flow
Increased Profitability
When you lower costs, you increase your profitability. This assumes, of course, that you maintain your current pricing levels. It also assumes that the savings you achieve aren’t absorbed by some other expense.
As mentioned earlier, higher quality can give you the ability to charge a premium for your product. The result of which also helps to make you more profitable.
When you increase your profits, you generate more cash with which to finance your business operations. As a result, you are less reliant on your local bank or investors for financing.
Key Benefits: Better cash flow, more funds available for reinvestment, less reliance on traditional sources of business financing
Better Working Environment
When you routinely work to refine your processes through continuous improvement, it has a positive impact on your culture. This is because it shows that you have high expectations and that your goal is to constantly make things better. This benefits everyone, not just the business.
It’s important that your staff also understands that this benefits them. One of the big benefits of continuous improvement is that it also makes life easier for your employees.
Key Benefits: Happier employees, less stress, less workplace drama
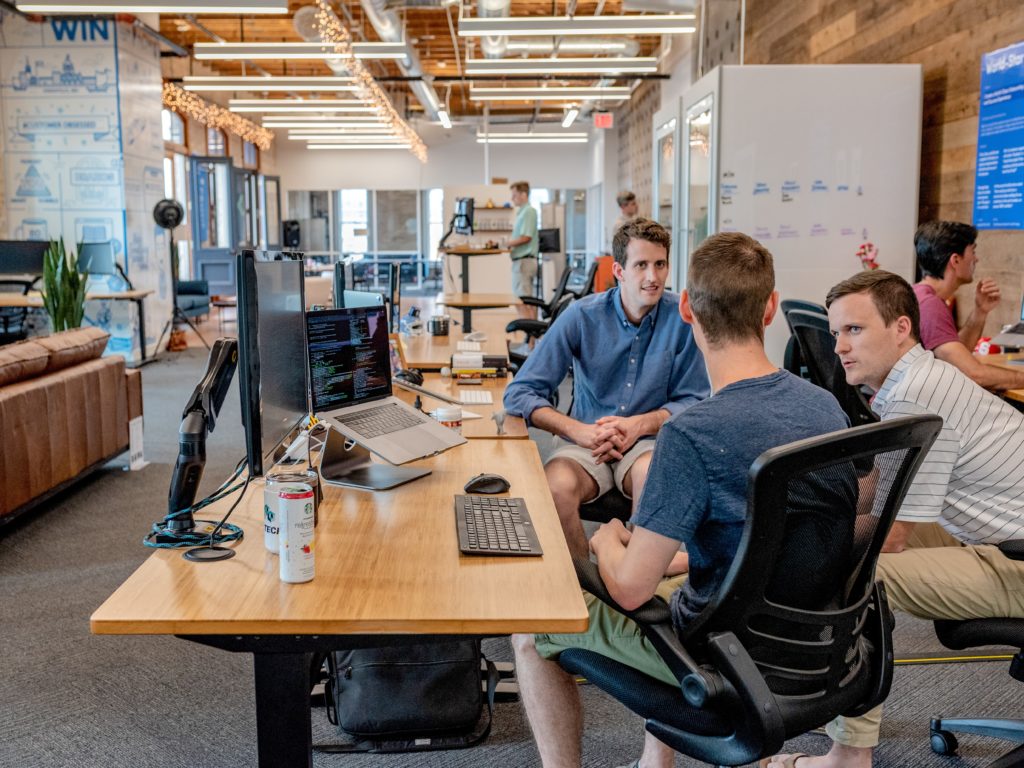
Happier Employees
Better working environments result in happier employees. Your continuous improvement efforts make their lives easier. When they notice this, it’ll be apparent in their demeanor. Not only is this good for morale, but countless studies have shown that happy employees are more productive and provide better customer service to your clients. This is a win-win-win.
Also, let’s not forget that happier employees are less likely to create conflict with others. If you include less drama, then this is a win-win-win-win.
Key Benefits: Easier to recruit new staff, higher retention rates, higher productivity, better customer experiences
Lower Employee Turnover
Happy employees typically don’t choose to leave their places of employment very often. This provides stability to both you and your staff.
It also results in tremendous cost savings. As a general rule, the cost to recruit, hire, and train someone, then get them up to speed, is usually around 25-30% of their annual compensation.
Now, add the intangible costs of less experienced staff. When you do, you’ll see that increasing your employee retention rate has a huge financial impact on your business.
Key Benefits: Reduced cost to recruit and train, higher institutional knowledge, more stability
Improved Culture
Culture is something that many in the business world talk about often. And it should be because Culture is what drives an organization to be what it can be.
However, it’s important to remember that you can’t just “create” culture. It comes from the top. Specifically, company culture comes from the actions of the business’s leadership. More simply put, a company’s culture is defined by the business owner’s actions.
When you focus on improving your processes, you create a culture of continuous improvement. Unfortunately, this doesn’t happen overnight. Rather, it takes time, but the end result is a culture in which your staff believes in doing the best they can.
This is the behavior that you’ve been reinforcing by prioritizing continuous improvement. As a result, you’ll see a direct improvement in the customer experience.
Key Benefits: Better teamwork, more desirable place to work, more effective collaboration, better customer experiences
Better Customer Experience
It’s no secret that happy employees provide better customer service. When you combine that with a higher quality product, fewer returns and faster delivery times, you have a recipe for a fantastic customer experience.
Imagine how much easier it would be to sell your product if you had hundreds of raving fans singing your praises.
Key Benefits: Better brand reputation, increased market position, more return customers
Increased Brand Reputation
All of this combines to increase the reputation of your brand. Building a successful brand is the pinnacle of business. Imagine if you could make your brand as recognizable as Coca-Cola, Microsoft or NASCAR. Wouldn’t that go a long way to helping you grow your business?
Successful brands have loyal customers. As a result, they’re able to introduce new products with ease by building on their prior success. They’re also able to leverage the same success to move into new markets.
Another benefit of your brand reputation is once again, the ability to charge a premium. As previously mentioned, when you can charge more for your product, it has a significant impact on your financial situation.
Key Benefits: Customer loyalty, less competitive pricing pressure, easier to break into new markets or introduce new products
In Conclusion
The benefits of continuous improvement are numerous. Many of these benefits are direct and tangible. Many are not. You can implement a formal continuous improvement program to achieve these benefits. Even if you choose to improve your processes on an informal, as-needed basis, you can still see dramatic improvements in your enterprise.
The key is to do something.